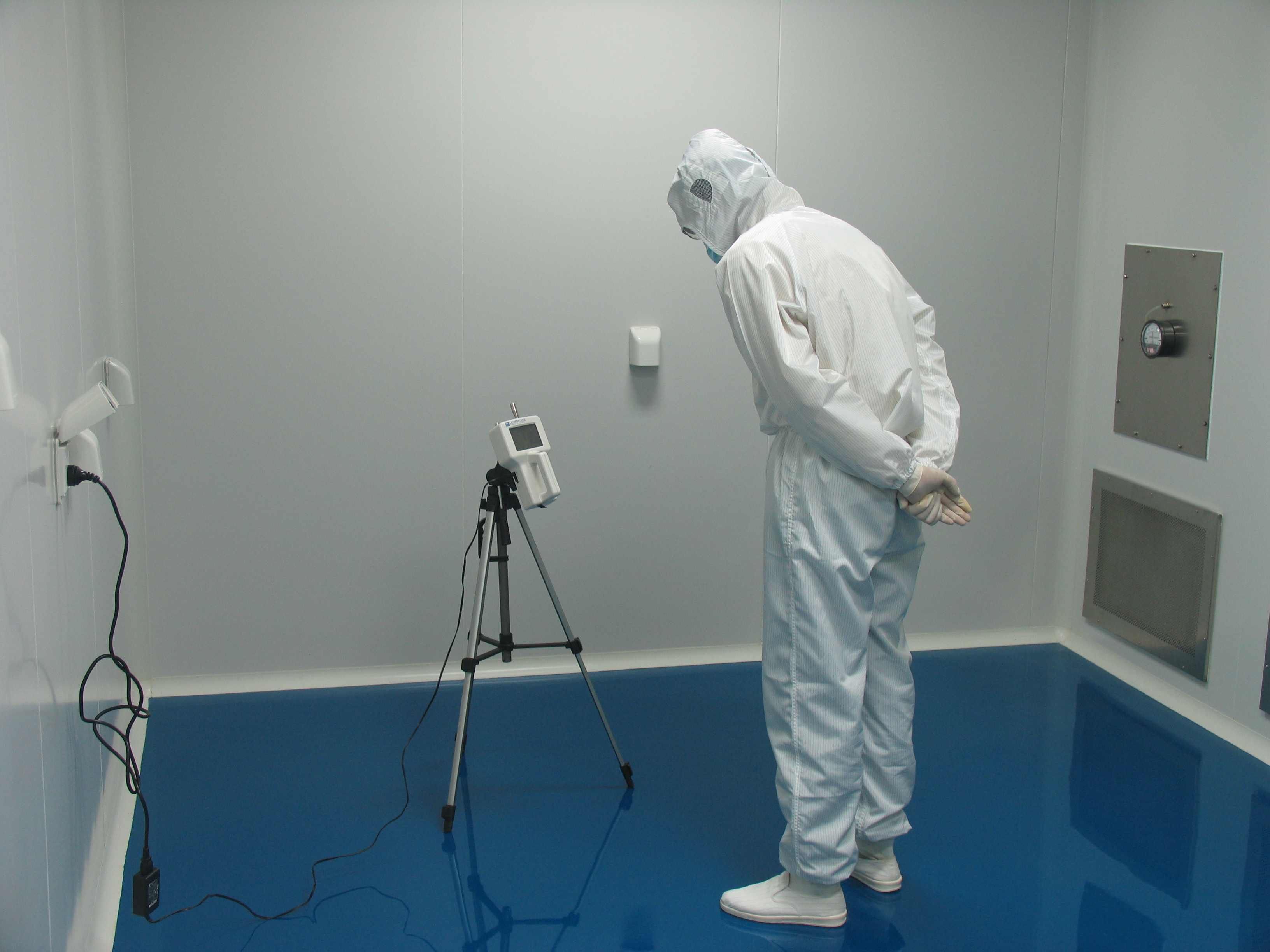
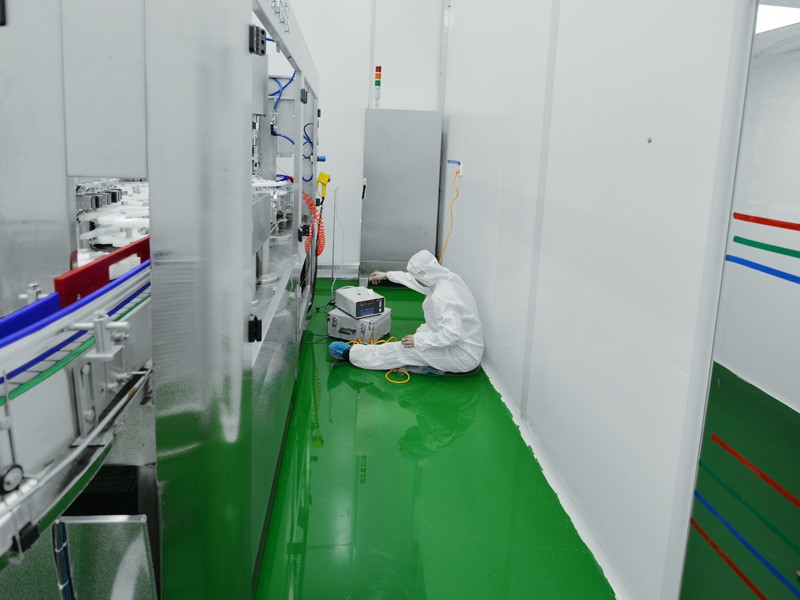
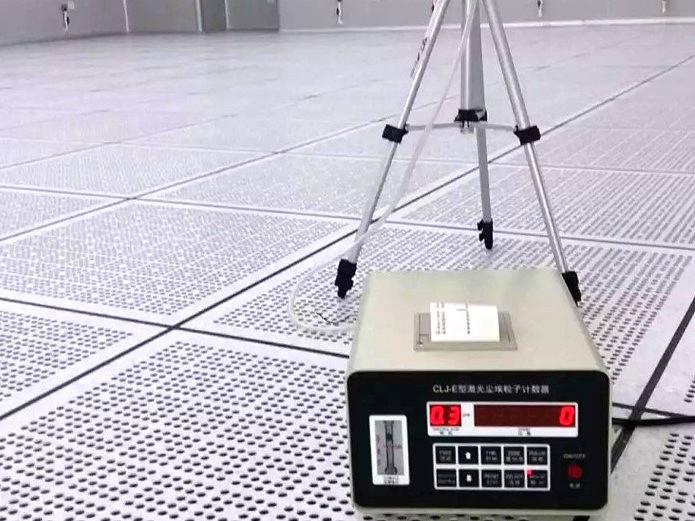
Pentru a respecta reglementările GMP, camerele curate utilizate pentru producția farmaceutică trebuie să îndeplinească cerințele de clasă corespunzătoare. Prin urmare, aceste medii de producție aseptică necesită o monitorizare strictă pentru a asigura controlabilitatea procesului de producție. Mediile care necesită monitorizare cheie instalează, în general, un set de sistem de monitorizare a particulelor de praf, care include: interfață de control, echipamente de control, contor de particule, conductă de aer, sistem de vid și software etc.
Un contor de particule de praf cu laser pentru măsurarea continuă este instalat în fiecare zonă cheie, iar fiecare zonă este monitorizată și eșantionată continuu prin comanda de excitație a computerului de lucru, iar datele monitorizate sunt transmise pe computerul stației de lucru, iar computerul poate afișa și emite un raport După ce a primit datele către operator. Selectarea locației și a cantității de monitorizare dinamică online a particulelor de praf ar trebui să se bazeze pe cercetarea evaluării riscurilor, necesitând acoperirea tuturor domeniilor cheie.
Determinarea punctului de eșantionare al contorului de particule de praf laser se referă la următoarele șase principii:
1.. ISO14644-1 Specificații: Pentru o cameră curată de flux unidirecțional, portul de eșantionare ar trebui să facă față direcției fluxului de aer; Pentru o cameră de curățare a fluxului non-unidirecțional, portul de eșantionare ar trebui să se confrunte în sus, iar viteza de eșantionare la portul de eșantionare ar trebui să fie cât mai aproape posibil de viteza de flux de aer interior;
2. Principiul GMP: capul de eșantionare trebuie instalat aproape de înălțimea de lucru și locul în care este expus produsul;
3. Locația de eșantionare nu va afecta funcționarea normală a echipamentului de producție și nu va afecta funcționarea normală a personalului în procesul de producție, pentru a evita afectarea canalului logistic;
4. Poziția de eșantionare nu va provoca erori mari de numărare din cauza particulelor sau picăturilor generate de produsul în sine, ceea ce face ca datele de măsurare să depășească valoarea limită și nu va provoca daune senzorului de particule;
5. Poziția de eșantionare este selectată deasupra planului orizontal al punctului cheie, iar distanța de la punctul cheie nu trebuie să depășească 30cm. Dacă există o stropire lichidă sau revărsare într -o poziție specială, rezultând rezultatele datelor de măsurare care depășesc standardul regional al acestui nivel în condiții de producție simulate, distanța în direcția verticală poate fi limitată să se relaxeze corespunzător, dar nu trebuie să depășească 50 cm;
6. Încercați să evitați plasarea poziției de eșantionare direct deasupra trecerii containerului, pentru a nu provoca un aer insuficient deasupra containerului și turbulenței.
După ce toate punctele de candidat sunt determinate, în condițiile mediului de producție simulat, utilizați un contor de particule de praf cu laser cu un debit de eșantionare de 100L pe minut pentru a proba fiecare punct de candidat în fiecare zonă cheie timp de 10 minute și analiza praful tuturor tuturor Puncte de înregistrare a datelor de eșantionare a particulelor.
Rezultatele de eșantionare ale mai multor puncte candidate în aceeași zonă sunt comparate și analizate pentru a afla punctul de monitorizare cu risc ridicat, pentru a determina că acest punct este un punct de instalare a capului de monitorizare a particulelor de praf adecvate.
Timpul post: 09-2023 august