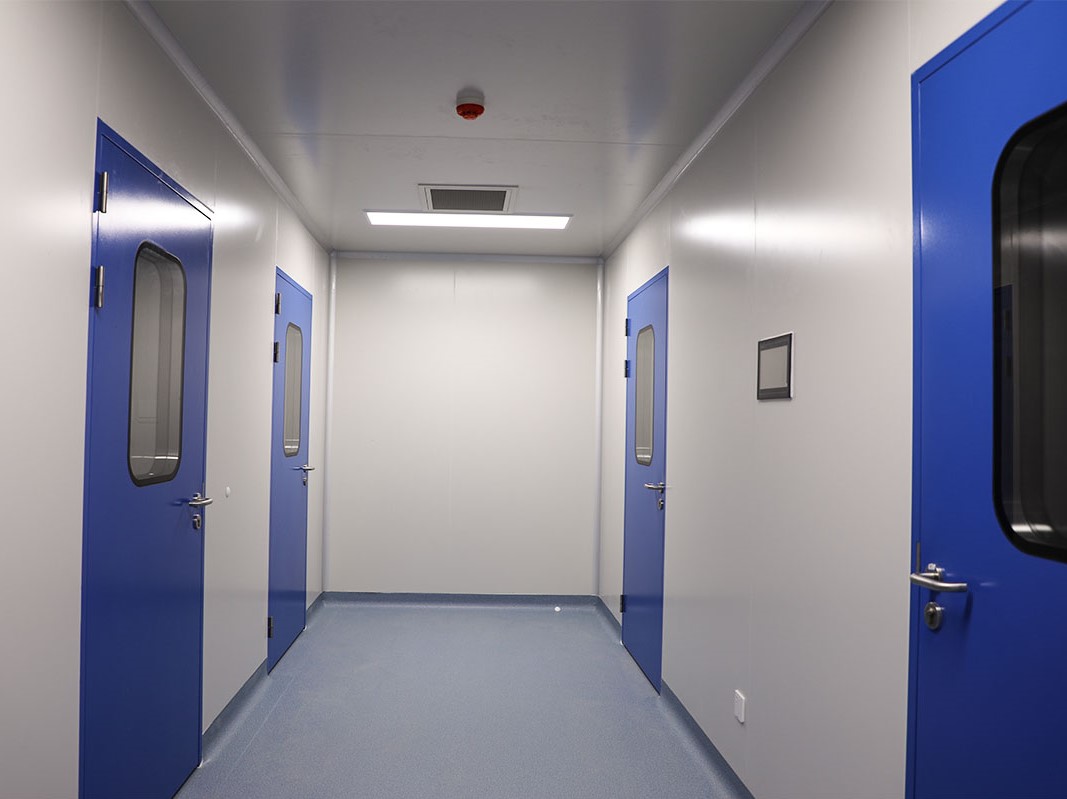
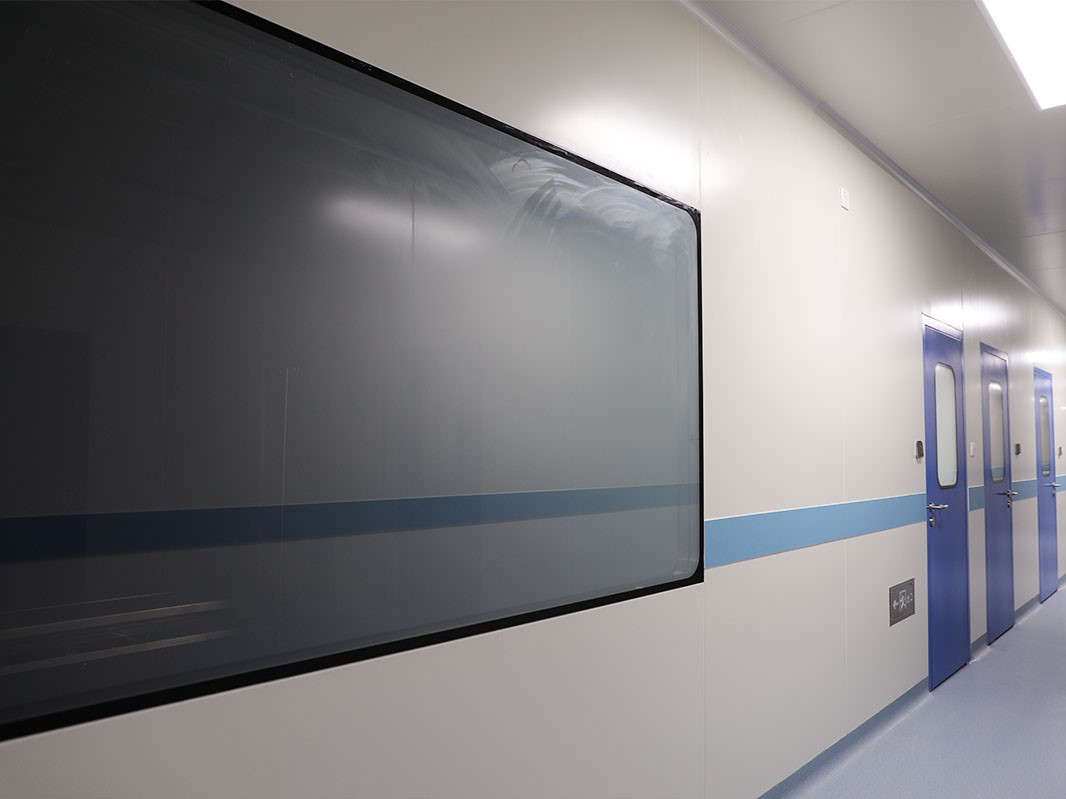
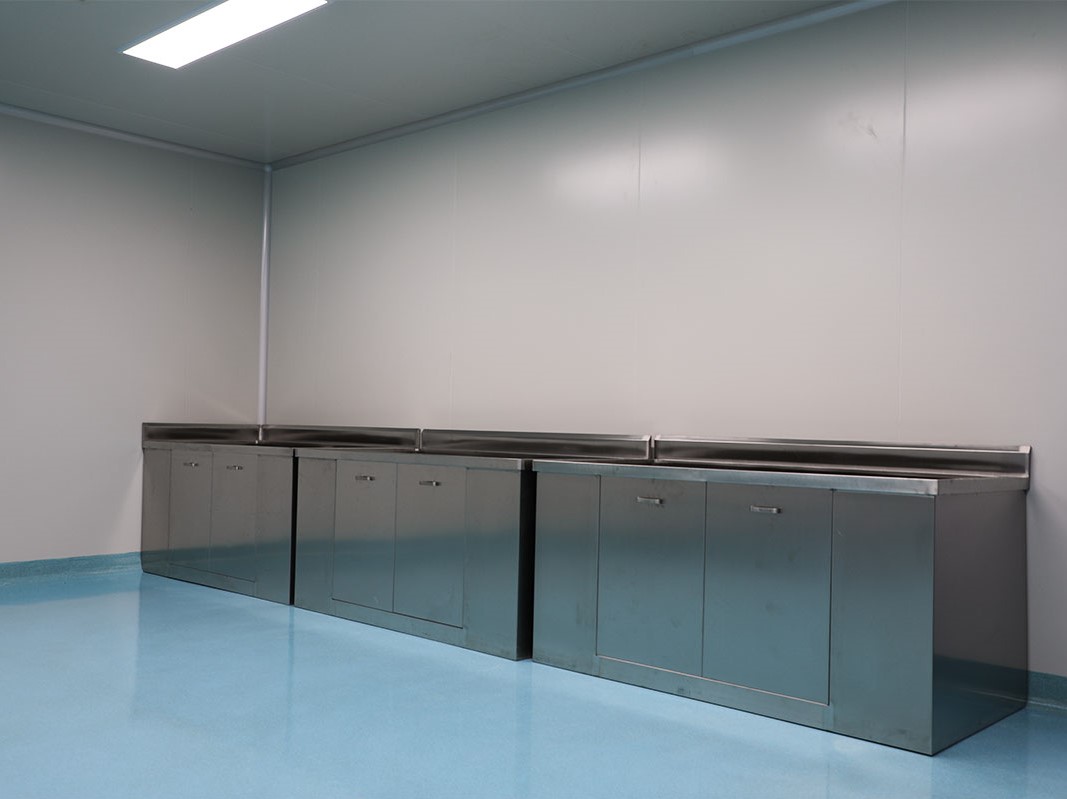
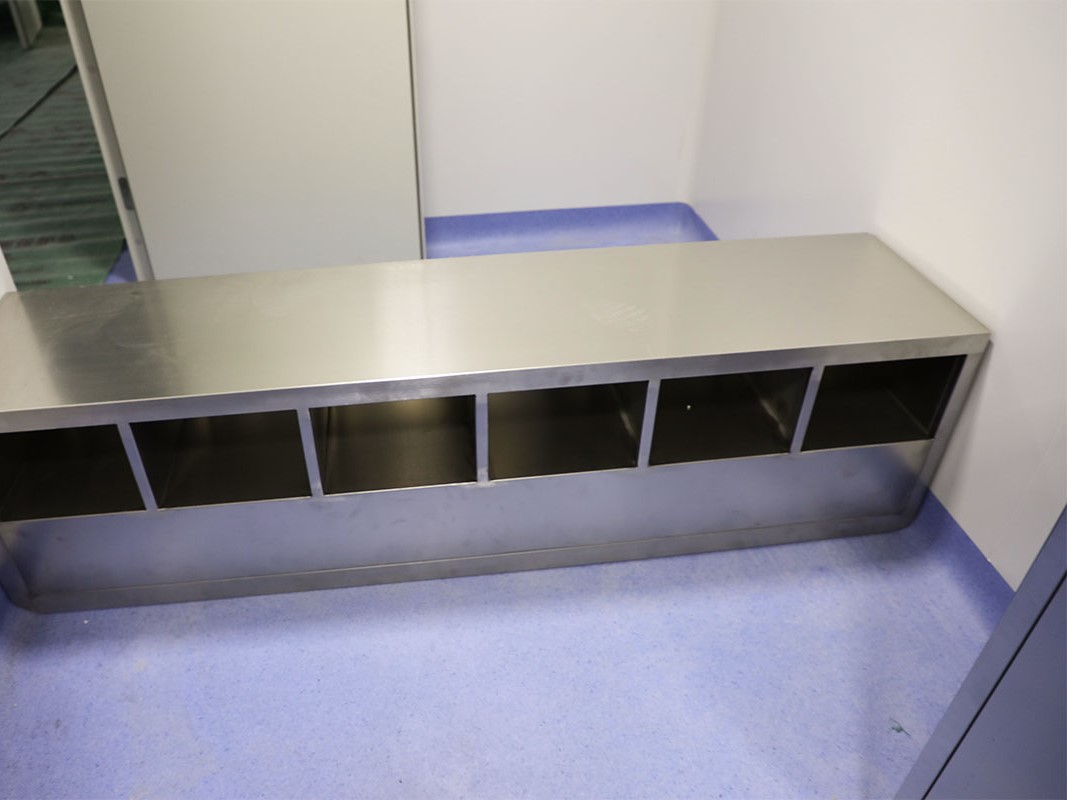
De la promulgarea sa în 1992, „bună practică de fabricație pentru medicamente” (GMP) din industria farmaceutică din China a fost recunoscută, acceptată și implementată treptat de întreprinderile de producție farmaceutică. GMP este o politică națională obligatorie pentru întreprinderi, iar întreprinderile care nu îndeplinesc cerințele din termenul specificat vor înceta producția.
Conținutul principal al certificării GMP este controlul de gestionare a calității producției de medicamente. Conținutul său poate fi rezumat în două părți: gestionarea software -ului și facilitățile hardware. Clădirea Clean Room este una dintre cele mai importante componente de investiții în instalațiile hardware. După finalizarea clădirii camerei curate, indiferent dacă poate atinge obiectivele de proiectare și îndeplinirea cerințelor GMP trebuie să fie confirmate în cele din urmă prin testare.
În timpul inspecției camerei curate, unii dintre ei nu au reușit inspecția de curățenie, unii au fost locali la fabrică, iar altele au fost întregul proiect. Dacă inspecția nu este calificată, deși ambele părți au obținut cerințele prin rectificare, depanare, curățare etc., de multe ori risipește o mulțime de forțe de muncă și resurse materiale, întârzie perioada de construcție și întârzie procesul de certificare GMP. Unele motive și defecte pot fi evitate înainte de testare. În activitatea noastră reală, am constatat că principalele motive și măsuri de îmbunătățire pentru curățenia necalificată și eșecul GMP includ:
1.. Proiectare inginerie nerezonabilă
Acest fenomen este relativ rar, în principal în construcția de mici camere curate, cu cerințe scăzute de curățenie. Concurența în ingineria camerei curate este relativ acerbă acum, iar unele unități de construcție au oferit cotații mai mici în ofertele lor pentru a obține proiectul. În etapa ulterioară a construcției, unele unități au fost utilizate pentru a tăia colțurile și pentru a utiliza unități de compresie de aer condiționat și ventilație mai mică din cauza lipsei lor de cunoștințe, ceea ce duce la o putere de alimentare nepotrivită și o zonă curată, ceea ce duce la o curățenie necalificată. Un alt motiv este că utilizatorul a adăugat noi cerințe și o zonă curată după pornirea proiectării și construcției, ceea ce va face, de asemenea, designul original să nu poată îndeplini cerințele. Acest defect congenital este dificil de îmbunătățit și ar trebui evitat în faza de proiectare a ingineriei.
2. Înlocuirea produselor de ultimă generație cu produse low-end
În aplicarea filtrelor HEPA în camere curate, țara prevede că pentru tratamentul de purificare a aerului cu un nivel de curățenie de 100000 sau mai mult, ar trebui utilizată filtrele la trei niveluri a filtrelor primare, medii și HEPA. În timpul procesului de validare, s -a constatat că un proiect mare de cameră curată a folosit un filtru de aer sub Hepa pentru a înlocui filtrul de aer HEPA la un nivel de curățenie de 10000, rezultând o curățenie necalificată. În cele din urmă, filtrul de înaltă eficiență a fost înlocuit pentru a îndeplini cerințele certificării GMP.
3. Sigilarea slabă a conductei sau filtrului de alimentare cu aer
Acest fenomen este cauzat de o construcție brută, iar în timpul acceptării, poate părea că o anumită cameră sau o parte a aceluiași sistem nu este calificată. Metoda de îmbunătățire este de a utiliza metoda de testare a scurgerii pentru conducta de alimentare cu aer, iar filtrul folosește un contor de particule pentru a scana secțiunea transversală, lipiciul de etanșare și cadrul de instalare al filtrului, identificarea locației scurgerii și sigilați-l cu atenție.
4. Proiectarea slabă și punerea în funcțiune a conductelor de aer de întoarcere sau a aerisirelor de aer
În ceea ce privește motivele de proiectare, uneori din cauza limitărilor de spațiu, utilizarea „returului de top al ofertei” sau a numărului insuficient de aerisire de retur de aer nu este posibilă. După eliminarea motivelor de proiectare, depanarea orificiilor de aerisire a aerului de întoarcere este, de asemenea, o legătură importantă de construcție. Dacă depanarea nu este bună, rezistența ieșirii aerului de întoarcere este prea mare, iar volumul aerului de întoarcere este mai mic decât volumul aerului de alimentare, va provoca, de asemenea, o curățenie necalificată. În plus, înălțimea ieșirii aerului de întoarcere de la sol în timpul construcției afectează și curățenia.
5. Timp insuficient de auto -purificare pentru sistemul de cameră curată în timpul testării
Conform standardului național, efortul de testare va fi început la 30 de minute după ce sistemul de aer condiționat de purificare funcționează normal. Dacă timpul de rulare este prea scurt, poate provoca, de asemenea, o curățenie necalificată. În acest caz, este suficient să se extindă în mod corespunzător timpul de funcționare al sistemului de purificare a aerului condiționat.
6. Sistemul de aer condiționat de purificare nu a fost curățat bine
În timpul procesului de construcție, întregul sistem de aer condiționat de purificare, în special canalele de aer de alimentare și retur, nu este finalizat într -o singură dată, iar personalul de construcție, iar mediul de construcție poate provoca poluare la conductele și filtrele de ventilație. Dacă nu este curățat bine, va afecta direct rezultatele testelor. Măsura de îmbunătățire este curățarea în timp ce se construiește, iar după ce secțiunea anterioară a instalării conductelor este curățată complet, filmul de plastic poate fi utilizat pentru a o sigila pentru a evita poluarea cauzată de factorii de mediu.
7. Atelier curat nu este curățat complet
Fără îndoială, un atelier curat trebuie curățat în detaliu înainte de testarea poate continua. Solicitați personalul de ștergere final pentru a purta haine de lucru curate pentru curățare pentru a elimina contaminarea cauzată de corpul uman al personalului de curățare. Agenții de curățare pot fi apă de la robinet, apă pură, solvenți organici, detergenți neutri, etc. Pentru cei cu cerințe anti-statice, ștergeți bine cu o cârpă scufundată în lichid anti-static.
Timpul post: 26-2023 iulie